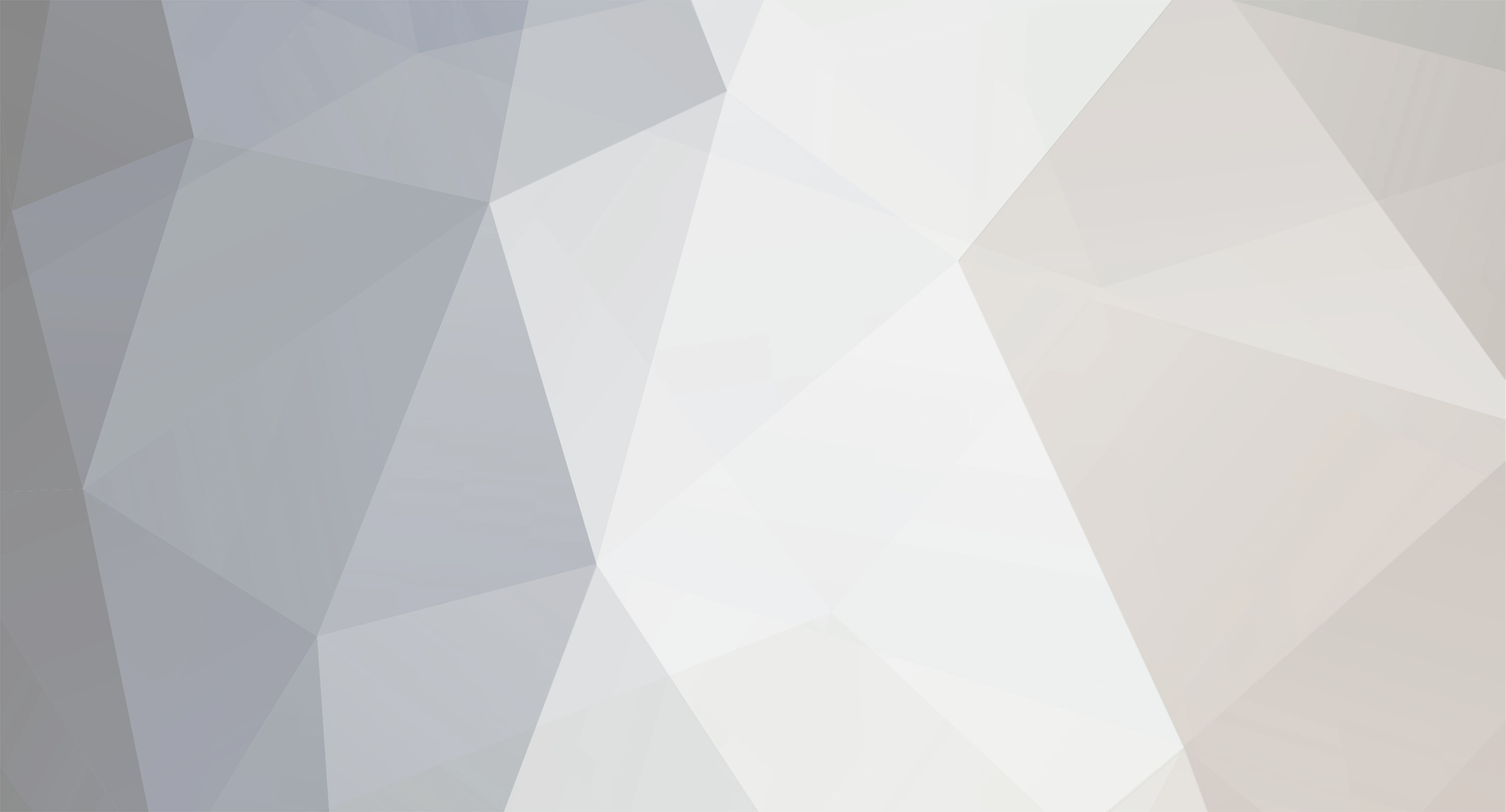
Chairs with Flares
Members-
Posts
17 -
Joined
-
Last visited
Profile Information
-
Real Name
Jeff
Chairs with Flares's Achievements
Newbie (1/14)
0
Reputation
-
Help Wantedke70 Oil Pressure Gauge
Chairs with Flares replied to Matt_23_ke70's topic in KExx Corolla Discussion
Hard to explain, but it felt different from how a correct NPT fitting seats. I've found NPT male ends (because of the taper) normally starts fairly loose and then seats up, whereas this was finger tight, gradually tightening/seating. That's the best I can explain, it just didn't feel 'right'. -
Help Wantedke70 Oil Pressure Gauge
Chairs with Flares replied to Matt_23_ke70's topic in KExx Corolla Discussion
I've also heard rumors that the thread is 1/8th NPT, but when I tried to thread an 1/8th NPT adaptor into my engine, it would bind up after a few turns. I know Japanese manufacturers also use 1/8th BSP, so that might be it. The difference between them is only one thread per inch, so it wil thread in tightly; which is what I did. I know it is not ideal, but as long as you are not undoing it frequently enough to wear the threads and use some proper thread sealant, it will hold up (mine has held up dailying 50km a day for the last year). I use an electrical Speco gauge on my 7K with a T fitting so I could keep the factory warning light. My other car (Mazda 2) has a Autometer mechanical gauge with a steel braided line, which reacts a little quicker than the electrical gauge. My other other car (MGB) has a factory mechanical Smiths gauge with a hard copper line which reacts just as quick. All my cars still have the factory oil warning light so I know when there is a large oil pressure drop. I really just use the gauges as a 'benchmark' to check for deviations from 'normal' pressure (low oil, dirty oil, worn components etc). With a mechanical gauge, I recommend using a braided line for peace of mind, although there is nothing inherently wrong with the nylon or copper line kits when used properly with the correct ferrules (most cars pre-1970's with an oil pressure gauge came factory with copper lines, and some go-karts use similar nylon lines as brake lines). Just make sure to tighten to spec, test and check regularly; it's better to fix a weep than wait for a failure. With an electrical gauge, it's better to mount the sender remotely and run a separate line to the block fitting. The senders are heavy and have a reputation of snapping off at the threads with the engine vibrations. -
The easiest way is to get a stiff straight bit of wire (cut the bottom length of a coathanger) and file the ends so they aren't sharp anymore. Poke it through the grommet between the existing loom, then tape the electrical wire/wires you want to run though to the end of the 'coat hanger' wire and pull it through. Coat hangers are great for anytime you need a straight piece of wire. Wire normally comes in a roll and is a pain to get dead straight.
-
Any signs of water in your oil? Looks like a milkshake when you drain the oil. Any signs of combustion gasses in your coolant? Start the car with the radiator cap off and see/sniff if there is any exhaust gasses bubbling up through the coolant. Are there any cooler/hotter spots on your radiator core? Any smoke on start up?
-
Just keep in mind that the throttle wheel needs around 90 degrees of movement from fully closed to fully open when locating your cable bracket. Ideally, you want the pedal travel to match the butterflies so that full pedal travel (bottomed out) equals fully open throttle, otherwise the throttles are open against the stop and you just stretch the cable. You can get around this with a throttle pedal stop on hte firewal adjusted to prevent the pedal from being pushed further and bending/stretching things. Adjustable bonnet stops/rubbers are good for this.
-
Do you have some parts of a linkage setup and are missing pieces? Or trying to work out which type of linkage to use? While a twin/multi DCOE setup needs adjustable linkages to sync the butterflies between the carbs, a single DCOE just needs the throttle cable to pull the throttle open. Googleing 'single DCOE' may give you some ideas... This is the generic type of linkage commonly used, that translates cable movement pulling on the bit sticking up to the throttle wheel (big round thing with holes). Even simpler would be just to have the cable pulling straight onto the wheel itself using a universal cable end. I have my twin Solex's set up to pull straight from the wheel this way with a 'tongue linkage' to sync the carbs (irrelevant for a single carb). You have to be careful doing it this way though; if the (full open) throttle stop is at the other end of the throttle shaft to the wheel, the shaft can be twisted when you stomp on the pedal since it's being pulled on one end of the shaft and a stopped on the other. The throttle wheel I used was only a semi-circle, so I made up a full throttle stop that the wheel hits at full throttle. (You can see on my setup as the cable pulls the throttle open, the wheel will hit the alloy tab when the butterflies are fully open. The cable attaches to the wheel by the way of a bolt with a hole drilled in it and some nuts, adjusted so it can pivot. You can also buy this, it's called a cable trunion. It's not fancy or shiny and has been called dodgy by some, but it's been working fine for two years without any issues. You'll want an extra throttle return spring to close the throttles too. You can get various lengths from Bunnings to hook up the the linkage to help pull the throttle shut. You want it working as close to (against) the cable as possible, and not on the other side of the shaft, again the twisting issue, although the spring tension shouldn't be high enough to cause damage. Just a thought for the long term (Mine has the throttle return spring on the other side between my two carbs, not optimal. Best would be pulling on the throttle wheel against the cable, I'll sort that out someday...)
-
It was because I had the leads for cyl 2 & 3 swapped. I was just curious why ALL of the cylinders were spitting and popping; after all, cyl 1 & 4 should not be affected right?
-
Ebay After Market Head Lights - Ke20
Chairs with Flares replied to cam_ae92's topic in KExx Corolla Discussion
They will fit any car that came out with the generic 7in round sealed bean 'H4' light. The housings are all the same, it's just the mounting brackets that vary, so yes, they will fit. $250 seems a bit steep, you should be able to get something off ebay from the US and have it work out cheaper even with shipping. -
So after replacing the plugs, I got the leads mixed up between cylinders 2 and 3. Needless to say it could barely hold idle and backfired through the carbs. The thing is; I'm running twin Solex sidedrafts (7K with electronic distributor) and there was backfiring from all 4 cylinders/carb throats, even though only two leads were swapped. I would have thought that only cylinders 2 and 3 would be backfiring, while 1 and 4 would still be running fine since it has it's own fuel delivery and timing correct. Anyone with ideas?
-
Need Help/advice With Engine Conversion
Chairs with Flares replied to 86RollaWagon's topic in KExx Corolla Discussion
I have/put a 7K into a (now mine) KE30, so I don't know how much will relate over to the KE70 in terms of measurements. It was put together on a budget, so we re-used as many parts as we could. The rear of the sump will not clear the center tie rod (steering box setup on KE30) buy about 10mm. We heated and gently 'massaged' the sump with a hammer, a little at a time until it fit. There were 3 of us and we took it slowly, pulling and fitting the motor 3 or 4 times, each time removing and heating/reshaping the sump until we got the clearance we needed. It sounds dodgy and the 'proper' way would be to have it cut and welded with a recess, but the end result was the same, no cracks or leaks and a sump that seals up against the block. No combination of left/right 3K/4K mounts would have the mounts fit flush with the crossmember. We ended up shortening the passenger side mount about 7mm by cutting and rewelding, then shimming the bottom (where it bolts to the crossmember) about 4mm with some steel plate cut to match the mount. There was a lot of experimenting with shims and lengths to get the mounts to sit flush so the rubber wouldn't be twisted. The 7K mechanical fuel pump had a return fitting back to the tank, which I didn't have on the KE30 tank, so that was replaced with the 3K mechanical pump which bolts straight in and turned out was enough to feed the twin solex carbs. Now for the fun part; driving experiences. My setup is just the stock 7K (I think, not sure if it has a cam, if it did, it's pretty mild) with twin Solex sidedraft carbies and a header, with a 4speed K40 behind it. The motor is all lowdown torque and there's no point revving it much past 5100RPM. That said, there's no need to as it will pull smoothly without lugging almost from idle. This means in 4th gear, it will pull from about 30kph without lugging. I run the stock 13in steelies with 175 profile economy tires and in the wet, it will spin up both rears (stock open diff) in second gear under power. Not clutch kicking, not bang-shifting, just a smooth 1st-2nd then plant it. In the dry I try not to shock the driveline as it's stock and probably won't take too much abuse before breaking the diff or trans from the additional torque. The standard 3K clutch started to slip after a while so I put in an Exxedy HD unit. From a standing start, it will juuust edge out a standard V6 VN Commodore to about 70-80kph where the Corolla runs out of legs and the Commy takes off, so while it's a good balance of power, it's still no rocketship. -
The thing with old steering boxes is that they spend most of their life in the center, so when it's good with the wheels straight, it will be too tight at full lock. Vice versa, if you adjust it to be good at full lock, there will be more play on center.
-
I had the exact problem when I replaced my clutch at the start of the year. The clutch pedal throw kept getting longer and longer and had to be constantly adjusted, and there was a light screeching noise with the clutch disengaged (pedal down). Otherwise, the car still drove fine. What I found to be the problem was that I installed the thrust bearing the wrong way around on the carrier. I put the flat side against the clutch fingers instead of the curved side. (In my defence, the old bearing was fitted this way and drove fine with no noise or play). The bearing clearly wasn't meant to bear any load this way as the outer and inner parts developed huge (2-3mm) of play relative to each other. This caused the outer part (the part that contacts the clutch fingers) to slide back far enough to scrape on the spring pins which hold the carrier to the fork. The bearing had worn a groove in the clips and I was lucky it didn't wear through them. That was the screeching sound. The outer bearing part becoming more and more separated made it feel like the cable was stretching as the whole fork/carrier assembly had to move further to disengage the clutch. Put a new thrust bearing in the correct way in and everything was sweet. Hope this helps. J.
-
Odd Clutch Behavior (Ke30-7K-K40)
Chairs with Flares replied to Chairs with Flares's topic in KExx Corolla Discussion
Kinda long, but I've had somewhat of a revelation. I've done about 300km driving to and from work on the new clutch setup now, and it seems the smoke is getting less everytine I check. I've narrowed the smoke down to my own mistake of over greasing the clutch splines (old habit from wrenching on old BMW motorbikes). I stuck my anal probe/boroscope and some fingers into the bell housing and found a film of grease on the pressure plate fingers, which could only be the included tube of grease in the clutch kit. Further testing of heating up some of that Exedy grease and comparing the similar smells (faintly rubbery) of smoke would suggest that it's the excess grease burning off. Being an HD clutch, I'm guessing that even if some got onto the friction materials, the additional clamping force of the pressure plate is still holding under torque. I don't really abuse the car too much as it still has the stock K40 and diff. No hard launches and I make sure everything is loaded up before the berries are given, so to speak. The thrust bearing is now making an occasional 'sshhh' noise on contact. Having a feel through the clutch arm hole (conveniently easy on a Corolla), the bearing feels fine with no play or crunchiness and my anal probe camera showed no discoloration from heat or anything irregular. I'll keep an eye/feel on it and see if anything develops. Thanks all for the input and happy travels. -
Odd Clutch Behavior (Ke30-7K-K40)
Chairs with Flares replied to Chairs with Flares's topic in KExx Corolla Discussion
I took off the sticker and cleaned up the gummy residue with acetone. There was a slight discoloration where the sticker was on thr pressure plate face though. -
From what I know, that plate is just that, a plate to stop the coolant coming out. Other engine variants have a welch plug there instead. Assuming you haven't done any damage from running hot, take of the plate and replace the gasket with sufficient sealant?