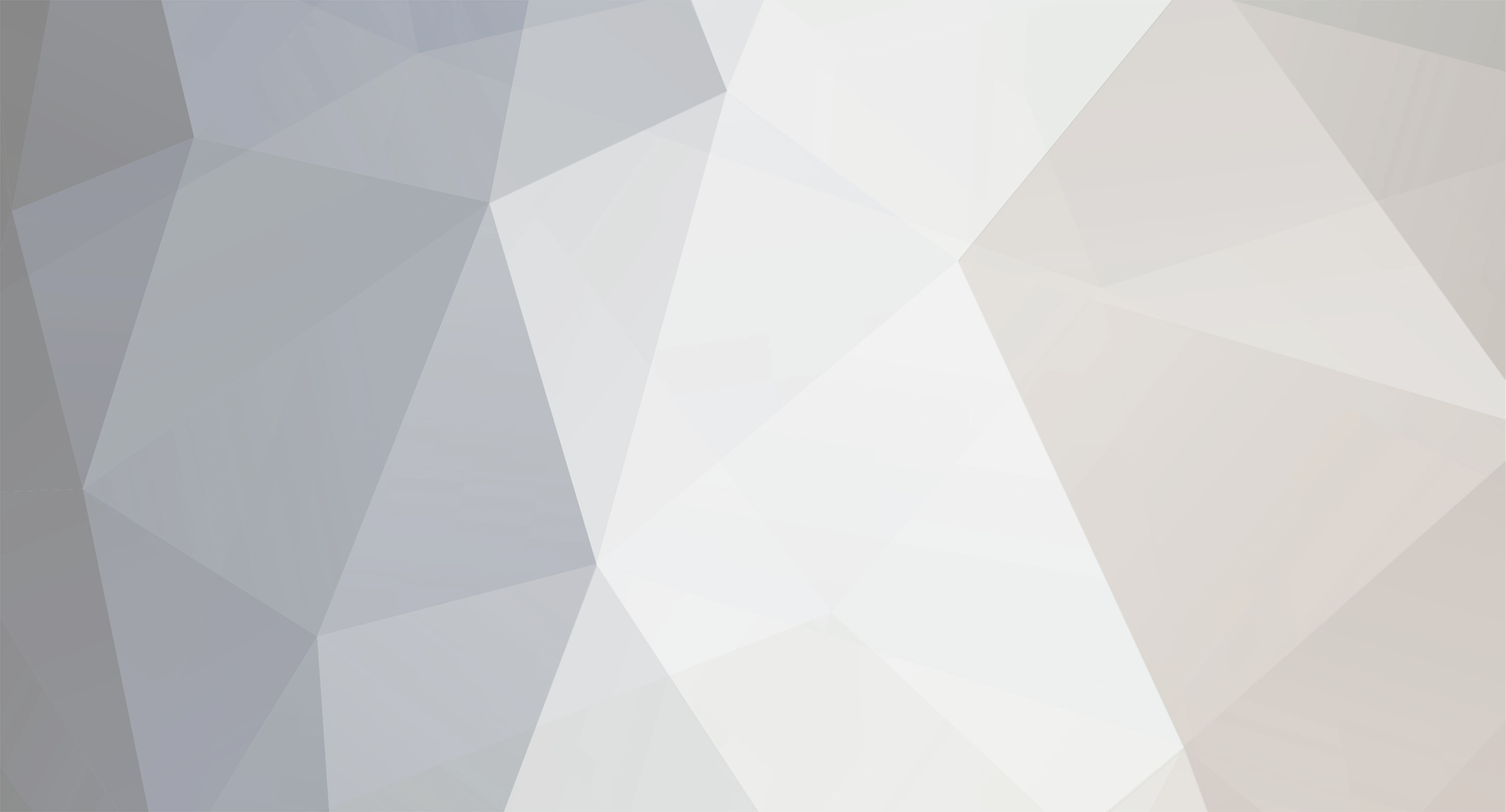
Jason
Regular Member-
Posts
1684 -
Joined
-
Last visited
Content Type
Profiles
Forums
Events
Gallery
Blogs
Everything posted by Jason
-
Welding I was lucky enough to be able to borrow a really cool automatic/electronic welding mask. They are worth it, if you can hire or get one for fairly cheap get it. There as clear as sunglasses until you strike an ark. Before you get you welder make sure you have • Angle grinder with grinding wheels and cutting wheels • Hammer. • Pliers • Snips (Thin sheet metal only – shaping) • Vice grips – MUST. Or a friend who's going hold it in place. Make sure you have every thing you need readily available to you. If you're hiring one you will want every last second with it. Make sure you work area is clean and the areas to be welder are not blocked by crap. Stuff will set on fire, like sound proofing, previous seam seals and that furry shit on the rear quarters. So a fire extinguisher/garden blower to put it out is always handy. Water is not such a great idea… You are using a high powered tool. OK get your piece of practice metal and make sure it doesn't have anything on its surface. Otherwise your ark might not start and you getting a dirty weld. Since your probably doing this for corolla metal (although its probably all the same), - the speed I used was about 8 with low voltage. See what you're comfortable with. I found it was easy to start with a high voltage ark until I got used to welding, then switched to low voltage. It gave a cleaner stronger weld with lower voltage. Any way, hold the torch (gun) with 2 hands. It gives you better control. With one hand on the grip and trigger, and the other on the ‘spout' like this.
-
Making the Replacement Sheets. For flat panels, like under the car and straights. The microwave sheets come in handy. • Measure the area to replace, then add a couple of cm. • Cut a sheet of metal to apox. the same dimension. • Now as good as you can, hold the sheet up to the space on the body and trace around it. • Get your grinding wheel and start to get close to the out lined shape. But don't take it all off, you cart ungrind it back on. • Test fit it. If it doesn't fit in, grind a little more off. • Repeat until it fits snugly into the designated area. This is MUCH easier using thinner material such as the door skin. You can precisely cut it with you snips. So instead of using the grinder. My 1st one took me ½ hr to get right. That's using microwave metal. I kept practicing until I got down to 5mins. So now do this for every hole you have! Should be fun… You might be wondering about how to do those bits were there's a lot of body creases :) Divide the working area up so you only dealing with 1 flat at a time, even though the body has a gentle curve that can be fixed with body filler later. INSERT PIC HERE
-
Crash Course in Seam Welding. All you need to know to start welding :) I decided to write this because of the lack of good, detailed documents on line on how to weld. The only experience was about 1 day of stick welding. Which no one taught me how to use. This time I got some help by a professional boiler maker. So I'm passing it on to help 1st time welders. The first part will go through removing rust out of panels and prepping it for welding. This should get you to the stage were you can fill over the panels with bog. Things you will need. • MIG welder • Welding mask if you don't want eye sunburn. Yes it hurts. • Tin snips. • Sheet metal. I used a microwave shell, good for strength, not so good for shaping. Door skins are great, go down to you wreckers and cut one up with some snips. • Vice grips. Spend the money, cheap ones are crap and will break • Pliers • Hammer • Block of wood • Angle grind o Grinding Wheels o Cut off wheels Removing the Rust • Cut it out. Use a fine cut off wheel. For areas were the body will lose strength. Leave some in, and cut it out once you have welded another piece in. This will stop ‘soggy' and warped finishes. You have to get it ALL • Once you have got it all out, try to grind it to a flat line, this makes it easier when making your replacement panels. Notice relatively straight line and lack of focusing skills
-
Ive almost finished writing an article on how to reweld rust spots :)
-
Warning May Eat Dogs and Small Children does that intake horn want to be any bigger! And that turbo whistle is crazy
-
Looks cool, but everythings been done before :D *Jason thinks of cooler, more un-doable ideas * :D i want a HUD on the windscreen :)
-
rolfcopter :)
-
The 4agze caught my eye :D I didn't want to go FWD but i still wanted a relativity easy swap.. ! Ae71 :) Also there cheap for spare parts and got a sleeper look. I wanted a bogan spec Torrana V8 308 :D but then i though of fuel consumption + i couldn't even afford to buy one stock. And now i love all the old school rollas :D Dam Internet keeps cutting out :)
-
Well after having the welder for 3 days now, Ive completed 1 and 1/2 guard skins, front quarter rust spot and some under body rust. Today about the only day Ive been welding for more than 2 hours :) I'm happy they way my super ammeter welding came out
-
the only things it needs improving... is a super dark tint :)
-
O for f@$ks sake! Your right. Just got it out with some vice grips! :)
-
:P looks fuking tough!
-
Well got a welder, time to start repairng pannels :D Also i think the preivouse owner of my gze messed with the throtle body :P Its got this metal plate over what i think is ment to by an auxilery air bypass valve ? Can any one enlighten me?
-
easer said then done. I'm looking at the spedo assembly now. Its all built in and tamper proof.
-
-
I think I'm gonna get rid of the Km/h and rev/min. Becuse it messes the whole clean look up. Ive to 2 shinny sheets left. :P I would love not to be able to put the odometer back in. But is that defectable?
-
Put a hot chick in the back ground :P
-
Hmm interesting, because the red line of the gze start at about 8000rpm... As Fook said before are they layered? Because the shinny gloss looks real hot :P Ok, test fits with paper prints.
-
6. Turn the dial or layer 1 if you haven't named it back on Done :D The reason why i didn't clean the entire back ground up was that most of it is not seen 1cm below the straight line. HIJACKED! :P
-
5. Clean the back ground layer up. First turn you dial layer off so you can see easier. You can add a image now if you want.
-
-
-